Layered Process Auditing:
Layered Process Auditing, also known as LPA, is an increasingly popular quality tool developed for manufacturing management. When utilized properly, LPA will drive cultural change throughout an organization to improve quality and efficiency, reduce scrap and rework, and reduce customer rejections. But what exactly are Layered Process Audits?
Layered Audits represent a formalized system focusing time and energy toward insuring high-risk processes and error proofing devices do not exhibit a lot of variation and are working properly. A Layered Process Auditing system is comprised of three critical elements:
- A set of Audits focused on High-Risk Processes
- Layers of Auditors from all areas of Management who perform Audits
- A system of Reporting and Follow-up to ensure Containment as needed and drive Improvement
A Collection of Audits
This element of a Layered Process Auditing system is as simple as it sounds. Audits are simply an organized group of questions designed to examine a device or process. Audits in an LPA system should focus only on areas in the manufacturing process where deviation represents a high-risk for producing defective products. If, for example, you have an electronic scale that continually makes critical measurements for ingredients in a sensitive chemical compound, problems that affect the performance and calibration of the scale could quickly cascade into defective products or worse. It is therefore critical to monitor that scale and ensure that it remains within tolerances. A good LPA system will include an audit of this scale and ensure containment and corrective action is immediately taken if the accuracy of the scale is not verified or the scale has fallen out of tolerance.
Layers of Auditors
In an LPA system, your collection of audits is performed on a regular basis, at a predetermined frequency, by multiple layers of management from across the manufacturing organization. For example, the Shift Supervisor for each shift might perform the audit which examines our hypothetical scale once per shift. Another layer of management, which might include process engineers, manufacturing support personnel, or even human resources staff, would perform the same auditon a rotating basis along with the other audits in the system. By assigning a number of auditors to this layer and creating a schedule that rotates through the system's audits, the example audit might be completed by someone in the layer once per week or once per month. Yet another layer of management (the number of layers in an LPA system can vary greatly from facility to facility, based on your needs), might include the top management or even executive staff. Once again, this additional layer of auditors performs the same collection of audits at some set frequency on a rotating schedule, completing the example audit perhaps once a month or once a quarter.
Containment, Reporting & Follow-up
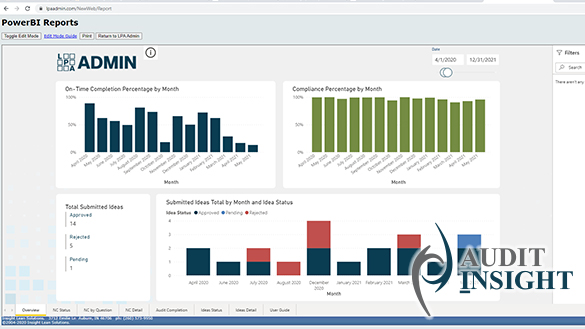
For a Layered Process Audit system to be truly effective, it must integrate action, analysis, improvements, and escalation. If an auditor finds a non-conformance while performing an audit, that auditor should not only record their finding, but also take immediate initial corrective action to ensure defective products are not produced or shipped. Information about the finding should be recorded and readily available to management for later analysis, improvements, and/or escalation, as required. With a good system for recording and reporting audit information, an LPA system provides an excellent tool for troubleshooting problem areas and identifying places which are ripe for improvement.
Though you may implement Layered Process Audits to satisfy a customer or company directive, effective LPA systems are designed, implemented, managed, accountable to, and owned by your participative manufacturing management group. A good LPA system is a highly effective tool for taking proactive control of manufacturing processes and improving product quality and the bottom line.